Pharmaceuticals
Japan Blood Products Organization Kyoto Plant
High-performance once-through boiler with reliable maintenance support
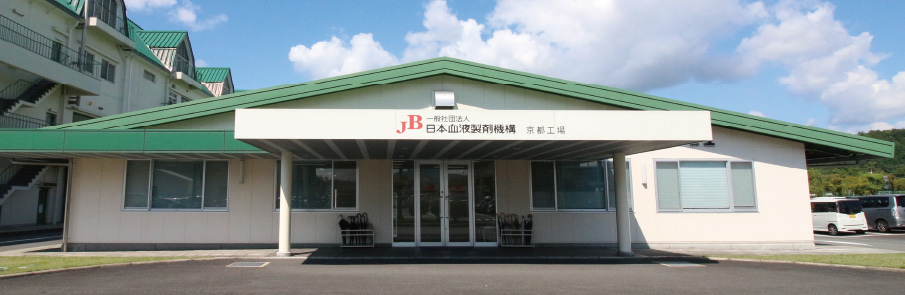
They were established in 2012 with the goal of achieving domestic self-sufficiency and a stable supply of blood donations. They convert blood donations of goodwill into plasma fractionated products and supply them to medical institutions that support those who need them. Their Kyoto plant is one of the largest manufacturing facilities for plasma fractionated products in Japan.
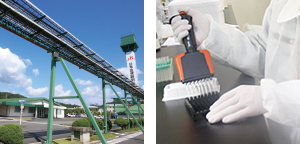
Reason for Selection
Boiler replacement along with pure water equipment renewal
Emphasis on maintenance support, not just products
We use boilers to produce “pure water” that is safe for the human body. The boilers are a piece of equipment that can never be shut down in order to provide a stable supply of pharmaceutical products to the medical field. We decided to replace our old boilers with new NTEC boilers after considering not only the energy efficiency and performance, but also the maintenance system. We were reassured by their sales and maintenance staff’s words, “You can trust us with our service!” The boiler replacement has reduced our fuel consumption and we are very pleased with the energy savings.
of facilities
NTEC’s Proposal
Once-through boiler
Super EQOS
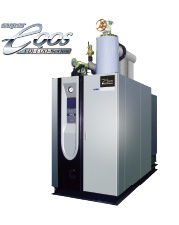
Compact and high-efficiency 3t/h once-through boiler
We proposed that they replace the old boilers (once-through boiler [2t/h] x 8 units) with new ones (Super EQOS EQi-3000NM [3t/h] x 5 units). This model produces the largest amount of evaporation as a small boiler, and we are confident in its efficiency and functionality. Since their boilers are used for the manufacture of medical products and they also pay great attention to the boiler water treatment, we installed a dissolved oxygen monitor for the feed water to the boiler system. We also provide the best maintenance and inspection services by checking the status of the boiler equipment and fulfilling their requests to make sure that the equipment is not shut down due to malfunction.
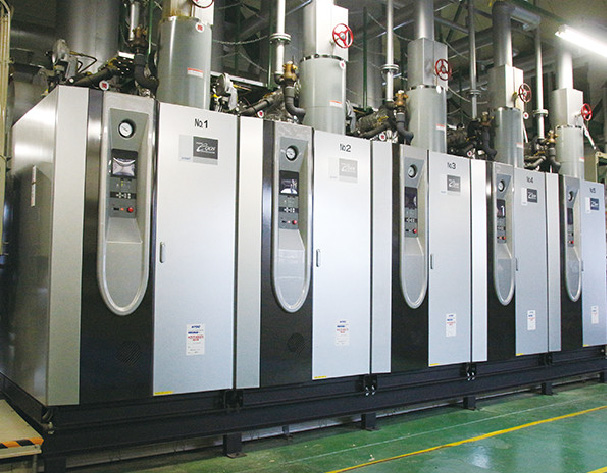
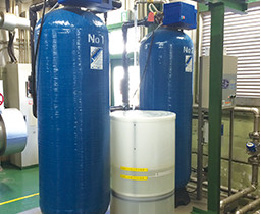
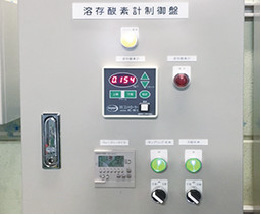
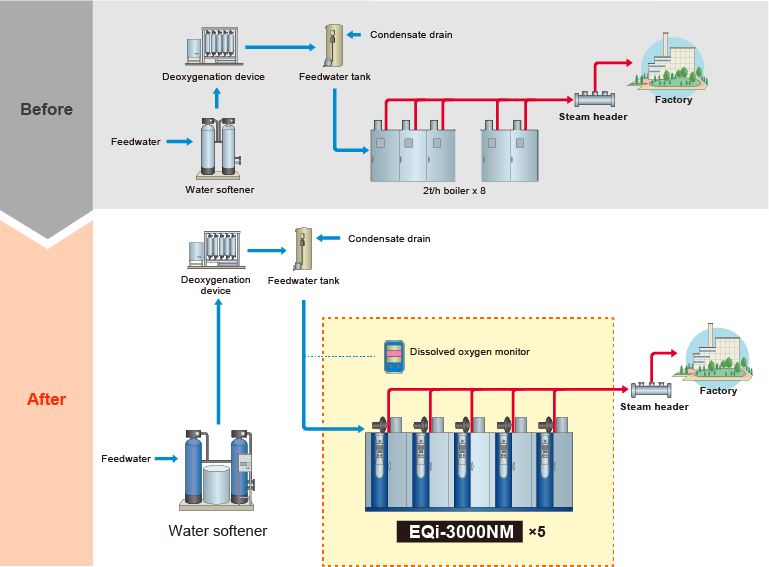
Customer Evaluation
They were concerned not only with the performance of a boiler, but also with safety and security. Initially, they were apprehensive about switching from our competitor’s boilers to ours, but thanks to the prompt and friendly response from our maintenance staff and the maintenance service that meets their needs, they are now using the boilers with peace of mind and satisfaction.
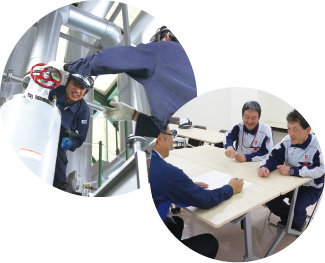
Related Products
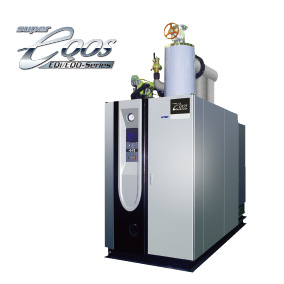
Once-through boiler Super EQOS
● Specification
Equivalent evaporation: 3,000 kg/h
Efficiency: 98 %
Max. working pressure: 0.98MPa
Fuel: Natural gas / Propane
Healthcare introductions and case studies
-
Ookuramaya Memorial Hospital
Vacotin Heater
EOL-100GN -
Thai Nakhon Pattana CO., LTD.
Super EQOS EQi Series
EQi-6001LM